Signs You Need Professional Packaging Machine Repair Right Away
Wiki Article
The Ultimate Overview to Packaging Equipment Repair: Maintain Your Workflow Running Smoothly
Comprehending the intricacies of product packaging equipment repair service is essential for maintaining optimum performance and decreasing interruptions. Regular maintenance not only expands the life of these machines yet additionally addresses typical issues that can impede performance.Value of Normal Upkeep
Regular upkeep of product packaging makers is essential for ensuring optimal efficiency and longevity. By applying an organized upkeep schedule, operators can identify potential concerns prior to they intensify into substantial troubles. This proactive method not only minimizes downtime yet additionally prolongs the lifespan of the tools, eventually bring about decreased functional prices.Normal examinations enable the evaluation of crucial elements such as belts, seals, and sensing units. Attending to wear and tear without delay avoids unforeseen failings that could interrupt production and lead to costly repairs. Additionally, routine upkeep aids ensure conformity with industry requirements and guidelines, cultivating a secure workplace.
Furthermore, upkeep tasks such as cleaning, calibration, and lubrication considerably improve maker effectiveness. Enhanced efficiency equates to constant item high quality, which is crucial for keeping consumer contentment and brand name online reputation. A properly maintained product packaging equipment runs at optimal speeds and reduces product waste, adding to total performance.
Typical Packaging Device Concerns
Product packaging equipments, like any kind of complicated machinery, can encounter a variety of usual concerns that may hinder their performance and effectiveness - packaging machine repair. One prevalent trouble is irregular sealing, which can lead to item wasting and waste if packages are not properly sealed. This often arises from misaligned elements or worn securing aspectsAnother constant problem is mechanical jams, which can occur as a result of international items, worn parts, or improper placement. Jams can trigger delays in manufacturing and increase downtime, inevitably impacting total efficiency. Additionally, electronic malfunctions, such as failure in sensing units or control systems, can disrupt procedures and lead to incorrect dimensions or irregular equipment actions.
Additionally, issues with product feed can additionally arise, where products may not be supplied to the packaging area constantly, causing disturbances. Wear and tear on belts and rollers can lead to suboptimal performance, calling for immediate interest to protect against further damage.
Recognizing these typical concerns is vital for preserving the honesty of packaging operations, making sure that equipment runs smoothly and successfully, which consequently assists in conference manufacturing targets and maintaining product high quality.
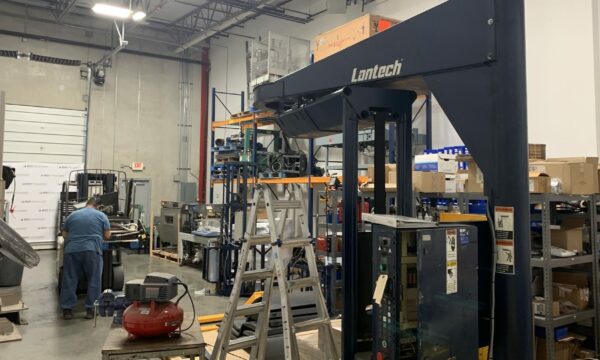
Fixing Techniques
Reliable fixing techniques are essential for without delay attending to issues that emerge with packaging machines. A methodical method is essential for determining the root reason of malfunctions and decreasing downtime. Begin by gathering details regarding the signs and symptoms observed; this may consist of unusual sounds, functional delays, or mistake codes displayed on the maker's interface.blog here Next, describe the device's guidebook for troubleshooting standards details to the design in inquiry. This resource can give important understandings right into typical concerns and recommended diagnostic actions. Utilize visual examinations to look for loosened connections, worn belts, or misaligned parts, as these physical variables frequently add to operational failures.
Execute a procedure of removal by screening private maker functions. For example, if a seal is not developing correctly, analyze the sealing device and temperature level settings to determine if they fulfill operational specifications. Paper each action taken and the outcomes observed, as this can aid in future troubleshooting initiatives.
Fixing vs. Substitute Decisions
When confronted with devices breakdowns, making a decision whether to change a packaging or fix maker can be a complex and essential option. This decision rests on a number of crucial variables, including the age of the machine, the level of the damages, and the forecasted effect on functional efficiency.
Firstly, think about the maker's age. Older devices might need more frequent repairs, leading to higher advancing prices that can exceed the financial investment in a brand-new system. Additionally, evaluate the extent of the malfunction. Small problems can frequently be settled promptly and economically, whereas substantial damage might require a significant monetary commitment for repairs.
Functional downtime is one more crucial consideration. If repairing the machine will cause extended delays, purchasing a new maker that supplies boosted efficiency and integrity may be extra prudent. Moreover, think about the accessibility of parts; if replacement parts are hard ahead by, it may be a lot more strategic to change the equipment entirely.
Ultimately, performing a cost-benefit evaluation that includes both long-lasting and prompt ramifications will help in making a notified choice that aligns with your functional goals and financial constraints. (packaging machine repair)
Safety Nets for Longevity

Trick precautionary procedures consist of routine lubrication of relocating parts, positioning checks, and calibration of controls and sensing units. Establishing a cleaning timetable to get rid of particles and pollutants from machinery can substantially minimize deterioration (packaging machine repair). Additionally, keeping continue reading this an eye on operational specifications such as temperature level and resonance can assist identify abnormalities early on
Educating staff to acknowledge indicators of wear or breakdown is another essential component of preventive maintenance. Empowering drivers with the expertise to do basic troubleshooting can cause quicker resolutions and reduce operational interruptions.
Paperwork of upkeep tasks, consisting of service records and evaluation searchings for, cultivates responsibility and facilitates notified decision-making concerning repair work and replacements. By focusing on safety nets, businesses can guarantee their packaging devices operate at peak performance, ultimately leading to enhanced productivity and lowered functional expenses.
Verdict
In verdict, the effective upkeep and fixing of packaging makers are critical for maintaining functional efficiency. Routine maintenance alleviates the risk of typical problems, such as irregular securing and mechanical jams, while systematic troubleshooting strategies facilitate prompt resolution of breakdowns. Careful factor to use this link consider of repair versus substitute choices adds to economical management of sources. By executing safety nets, companies can enhance maker durability and ensure undisturbed efficiency in product packaging procedures.Understanding the complexities of packaging machine repair is crucial for preserving optimal efficiency and decreasing disruptions.Normal upkeep of packaging devices is essential for making sure ideal efficiency and long life.Product packaging devices, like any complicated machinery, can come across a variety of common issues that might prevent their performance and effectiveness. If fixing the maker will certainly create long term hold-ups, spending in a new device that uses enhanced efficiency and reliability may be much more prudent.In conclusion, the efficient maintenance and repair work of product packaging makers are critical for maintaining functional efficiency.
Report this wiki page